Applications
Battery-less Goods Management Apps in Manufacturing Plants and Retail Industry
Battery-less, maintenance-free goods management revolution
Battery-less goods management applications can be used for parts management in manufacturing plants and inventory management in the retail industry. Through goods management, manufacturing plants can quickly respond to parts shortages, and retailers can prevent lost opportunities due to product shortages.
Table of Contents
What is a battery-less goods management application?
Goods management allows you to know if an object is in place and to find it quickly when needed, improving work efficiency and saving time and labor. Also, by checking the number of items remaining, inventory can be properly managed, preventing lost opportunities due to missing items and production delays due to insufficient parts during manufacturing.
RFID with FeRAM developed for our battery-less solution
LSI (battery-less LSI: MB97R8110) for RFID with FeRAM developed for our battery-less solution is equipped with a key matrix scan circuit and can detect switch ON/OFF using only wireless power from the reader/writer (R/W).
We will introduce an application example of battery-less goods management realized by detecting ON/OFF of switches.
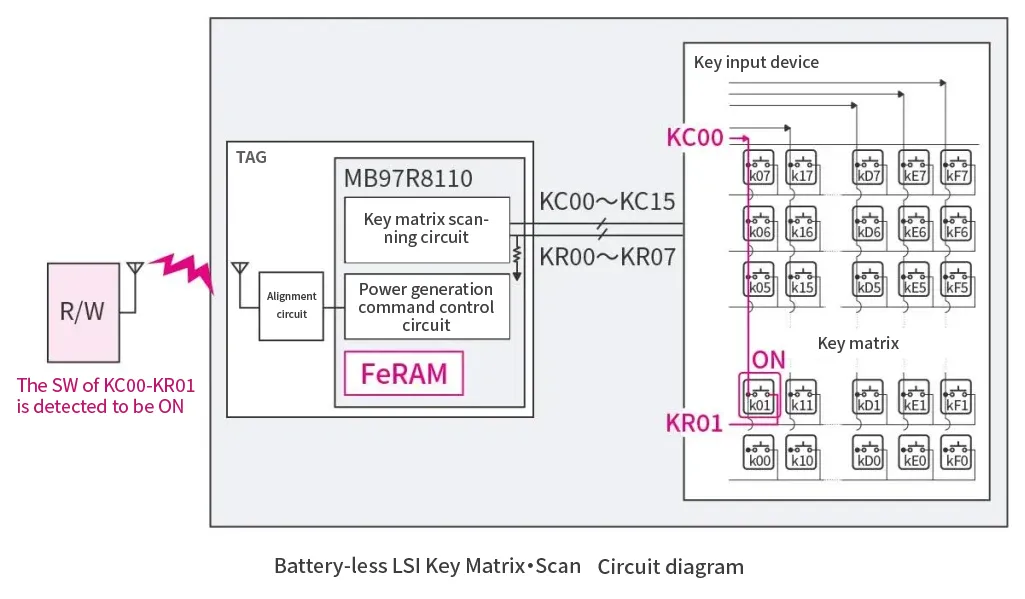
Application Examples of Battery-less Goods Management Application
1. parts management in a manufacturing plant
At a manufacturing plant, parts required for assembly are kept on shelves and are assembled by removing parts from the shelves. However, if parts are not properly managed, they may not be available in a given location. As a result, problems such as manufacturing delays due to the search for parts or production line stoppages due to missing parts may occur.
By using our LSI (MB97R8110), battery-less parts management can be realized. A fixture equipped with a switch is placed on the parts shelf, and our LSI (MB97R8110) is connected to the switch. When a part is placed on the shelf, the mounted switch turns ON, and by detecting the state of the switch using R/W, the inventory status of the part can be monitored. The fixtures equipped with switches placed on shelves are battery-less, so there is no need for maintenance such as battery replacement. The system also has the advantage of being able to instantly respond to changes in shelf locations because it uses wireless communication.
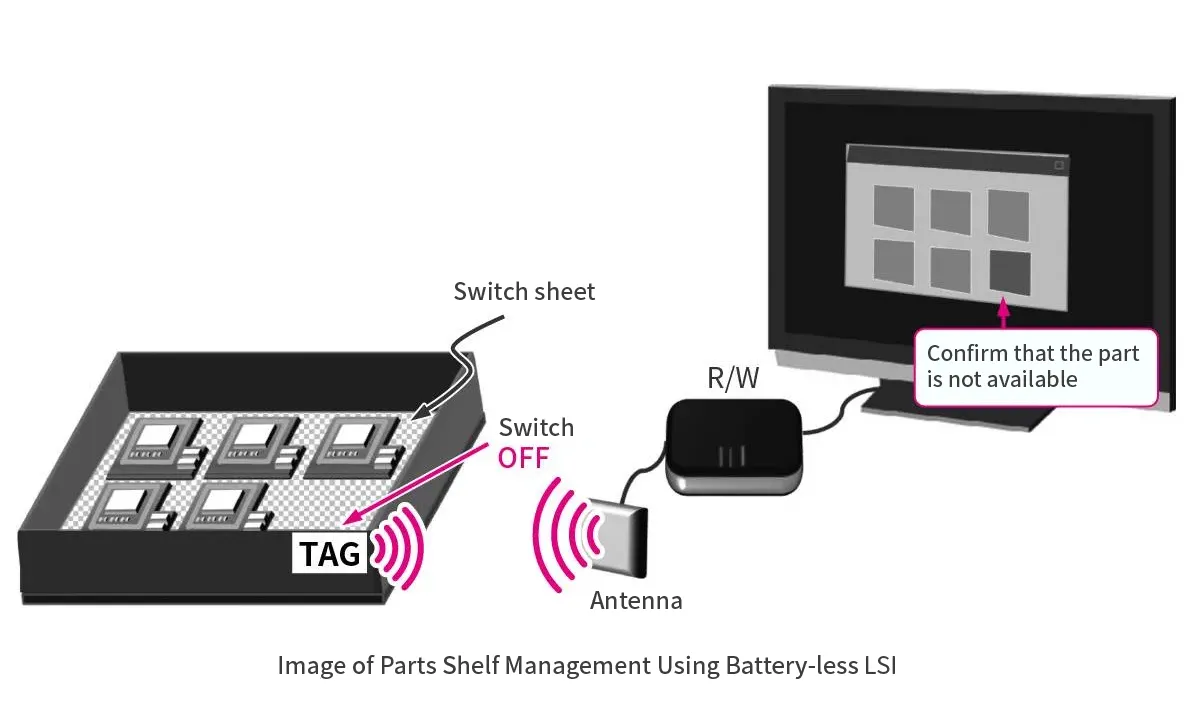
2. Inventory control in retail stores
Labor cost increases and other factors have led to increased labor savings in retail stores. If in-store inventory is not properly replenished, this can lead to lost sales opportunities and reduced customer satisfaction. When attempting to introduce an inventory control system, image analysis using cameras is considered, but the extensive construction work, installation costs, and the need to install the cameras in such a way that they do not create blind spots have become barriers to their introduction. By using an inventory management case that uses our LSI (MB97R8110), inventory management can be realized without the need for large-scale installation work.
Multiple switches are installed in the fixtures for product management. Since the number of switches turned on changes depending on the number of remaining inventory, the number of remaining inventory can be monitored by using our LSI (MB97R8110) to detect when the switches are turned on or off. The switch is powered wirelessly using R/W, so fixtures equipped with the switch can be realized without batteries and maintenance such as battery replacement is unnecessary. The use of wireless communication also has the advantage of allowing immediate response to location changes.
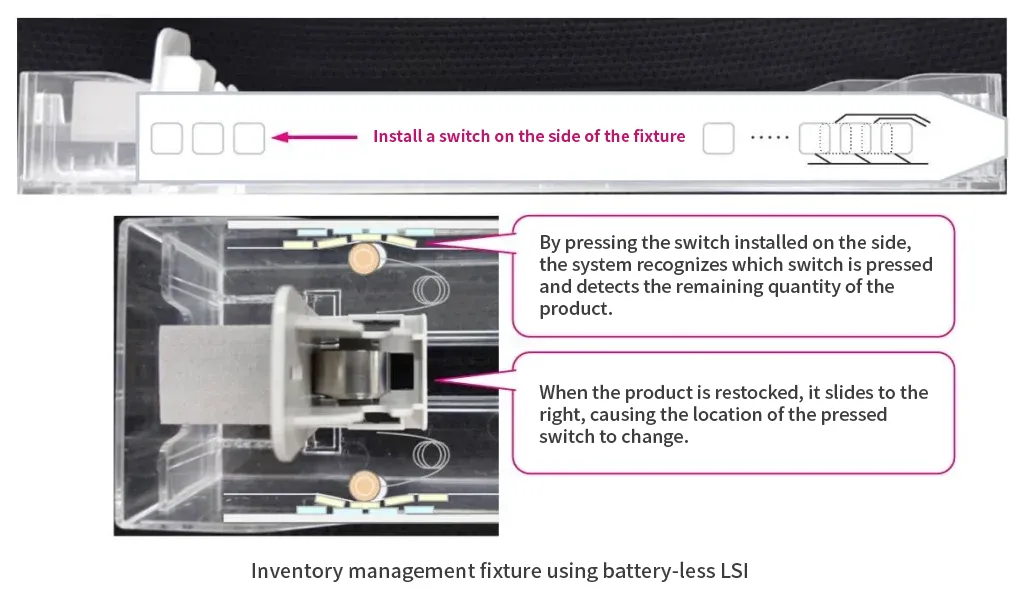
Video of Inventory Management in a Retail Store
3. Tool management
Tools are essential parts of on-site work, but they may not be properly managed. If tools are left unattended at a work site, it can lead to personal injury, and proper management is required. Confirming that tools are stored securely in the tool box will prevent tools from being left behind. Checking by the system, rather than by a visual list, prevents human errors due to omissions.
By using the Key Matrix Scan function of our LSI (MB97R8110), it is possible to check whether tools have been returned to the tool box or not. By detecting the ON/OFF of a switch installed in the tool box, it is possible to confirm that the tool has been stored in the designated place and prevent tools from being left behind. The tool box equipped with the switch can be realized without batteries, eliminating the need for maintenance such as battery replacement. In addition, since wireless communication is used, it can be carried around and checked at the work site.
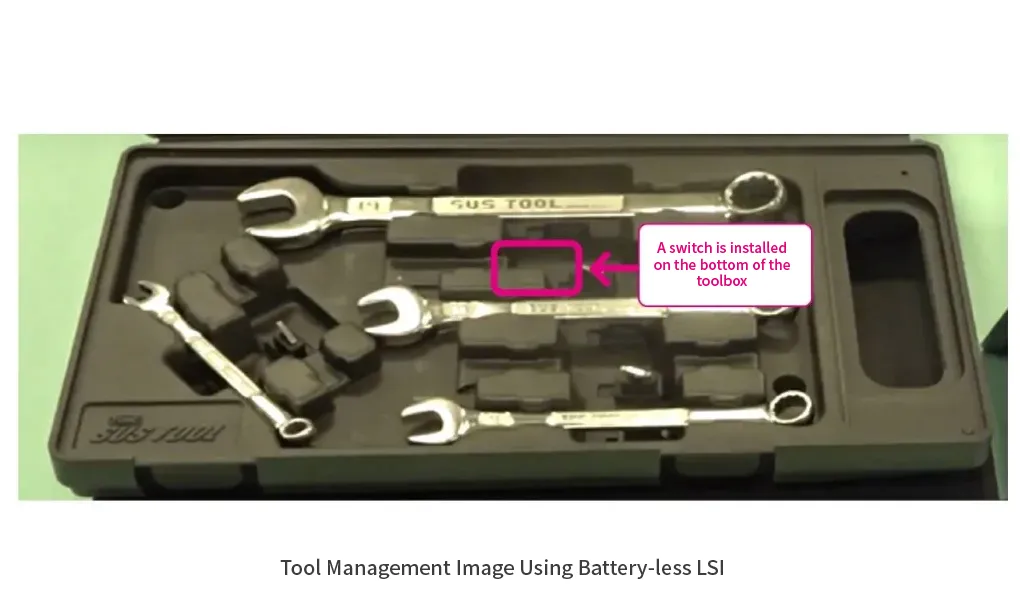
Tool management video