Applications
Example of adoption of FeRAM for automotive EDR
Capturing the Truth in 1/100th of a Second:
FeRAM's High-Speed Writing Keeps Information Immediately Before a Car Accident from Escaping
FeRAM is also used in the Event Data Recorder (EDR) in the electronic control unit (ECU) of airbags, which enables the recording and retention of detailed data that meets EDR regulations and helps determine the cause of accidents.
Table of Contents
What is an EDR?
An event data recorder (EDR) is an on-board accident recording device, which is built into the electronic control unit (ECU) of an airbag. This function records vehicle data such as speed in the time before and after an event such as a collision. As shown in the figure below, information such as vehicle speed is recorded in non-volatile memory in chronological order from 5s before the moment of the accident until the airbag deployment is completed.
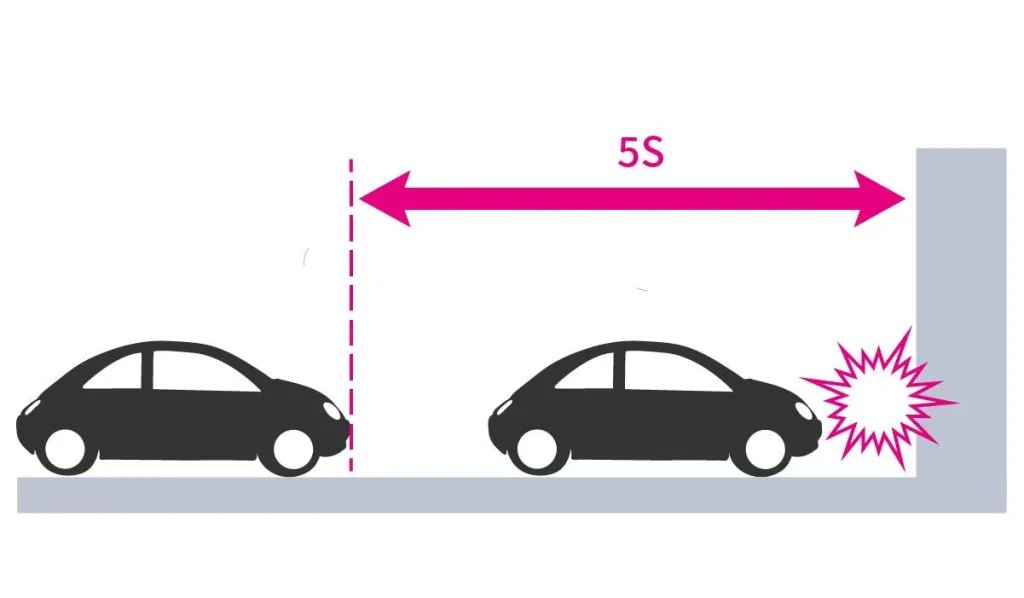
FeRAM Features and Benefits
Recording of detailed data to help determine the cause of an accident
EDR requires data to be written at high speed before and after an unforeseen event. Ideally, writing should start 5 seconds before the camera or sensor detects an accident, and be completed before the loss of power due to an accident, so that the data is protected. To achieve this, FeRAM, which can write data constantly and can complete writing in a very short time before power is lost, is optimal. In addition, a recommended value (up to 100 samples/s) is set for the number of data samples as well as the write time for EDR data writing. By using FeRAM for data writing, data before and after an accident can be accurately recorded, contributing to post-accident investigations and cause-finding.
The figure below shows an example of EDR data for a sample rate of once per second. Vehicle speed can only be determined every second and the exact timing of braking is not known.
The data recorded by the EDR includes changes in speed, speed indication, accelerator pedal position, and brake on/off. These data can be retrieved and analyzed after the accident to determine the driver's behavior immediately prior to the accident, the condition of the front and rear passenger seats, and the overall condition of the vehicle.
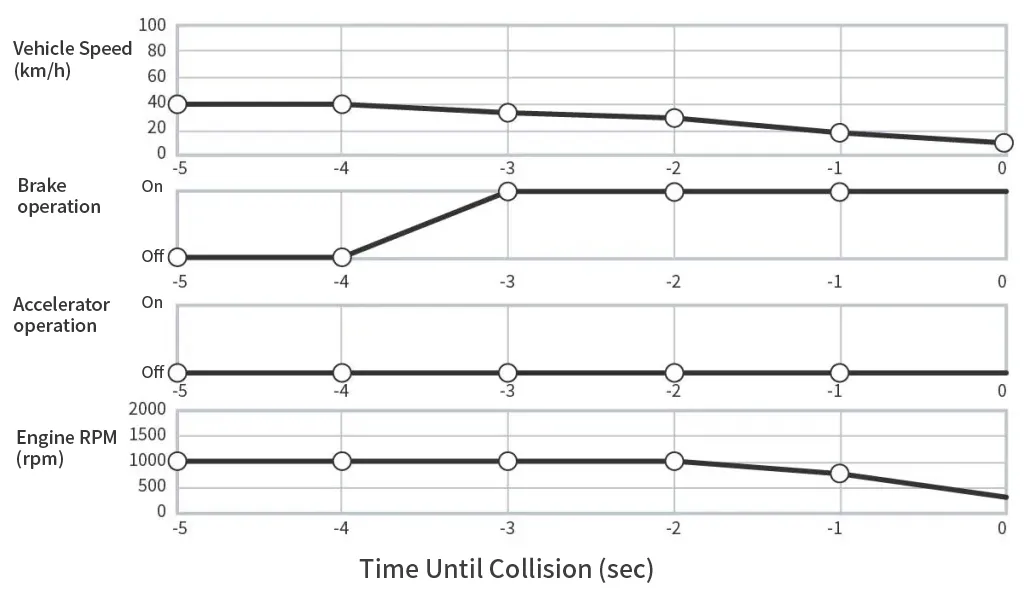
The figure below shows an image of data when vehicle speed is recorded at 100 samples/s and other data at 10 samples/s. Recording vehicle speed in 10 ms increments clarifies vehicle information. In addition, the braking action status can be grasped in more detail, and the driver's evasive action in the event of an accident can be accurately determined.
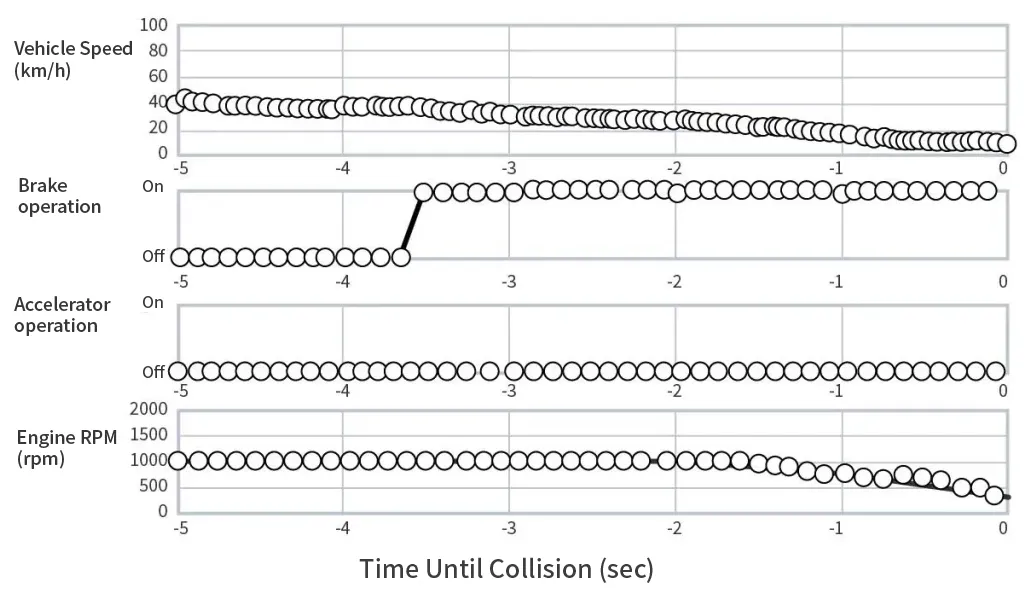
The following is quoted from the technical requirements of J-EDR by the Ministry of Land, Infrastructure, Transport and Tourism. The document also states that non-volatile memory is to be used, which requires a certain data sample rate and tamper-resistance of the data written to the memory. FeRAM can meet the requirements in both respects.
-
4.1.3 J-EDR shall capture and record data elements in any of the following cases
- (1) In the case of an accident involving airbag deployment, new accident data shall be captured and recorded for no more than two accidents. Thereafter, the recorded accident data shall not be overwritten.
-
(2) For accidents exceeding the activation threshold (vehicle speed change of 8 km/h or more within a 150 msec interval) or the activation threshold specified by the vehicle manufacturer and not involving airbag deployment, new accident data shall be captured and recorded for no more than two accidents, subject to the following conditions
- (i) If free space is available in the non-volatile memory in which the previous airbag non-deployment accident data was recorded, new airbag non-deployment accident data shall be recorded.
- (ii) If the free space in the nonvolatile memory where the previous airbag non-deploying accident data was recorded is unavailable, the vehicle manufacturer may choose to either overwrite the new airbag non-deploying accident data or not record it.
- (iii) The nonvolatile memory in which airbag deployment incident data is recorded must not be overwritten by new airbag non-deployment incident data.
Data available up to the last moment when power is turned off
FeRAM's high write endurance makes it ideal as a data buffer: events are continuously recorded in FeRAM while the MCU is running, and because FeRAM is nonvolatile, data is retained even when the power supply runs out. Thus, the latest data is not lost even if the power supply breaks; writing data directly to FeRAM eliminates the need to transfer data from SRAM to EEPROM or flash memory. This eliminates the need for additional power to retain data until the last moment.
The following example shows the voltage and time lapse when data is written to a 1 Mbit SPI FeRAM. Comparing the datasheets of FeRAM for 1Mbit SPI, which is commonly used in industrial applications, with those of EEPROM and NOR FLASH, the cycle time is 120ns, 5ms, and 0.4ms, respectively. Assuming that the expected time from normal operation until the voltage drops to a level where memory operation is no longer possible is a few milliseconds, EEPROM can only log once and NOR FLASH several times during this period, while FeRAM can log several thousand times. In the case of EEPROM and NOR FLASH, the data immediately before a collision occurs is coarser than that of FeRAM, and the data is also less accurate than that of NOR FLASH. In the case of EEPROM and NOR FLASH, the last data may be coarser than that of FeRAM, and data writing may be completed at a voltage lower than the minimum operating voltage, which may cause some data to be incorrect.
Note: When NOR FLASH is continuously written in units of 1 page (256Byte), data must be erased for 30ms for each minimum sector (4KByte) before being written.
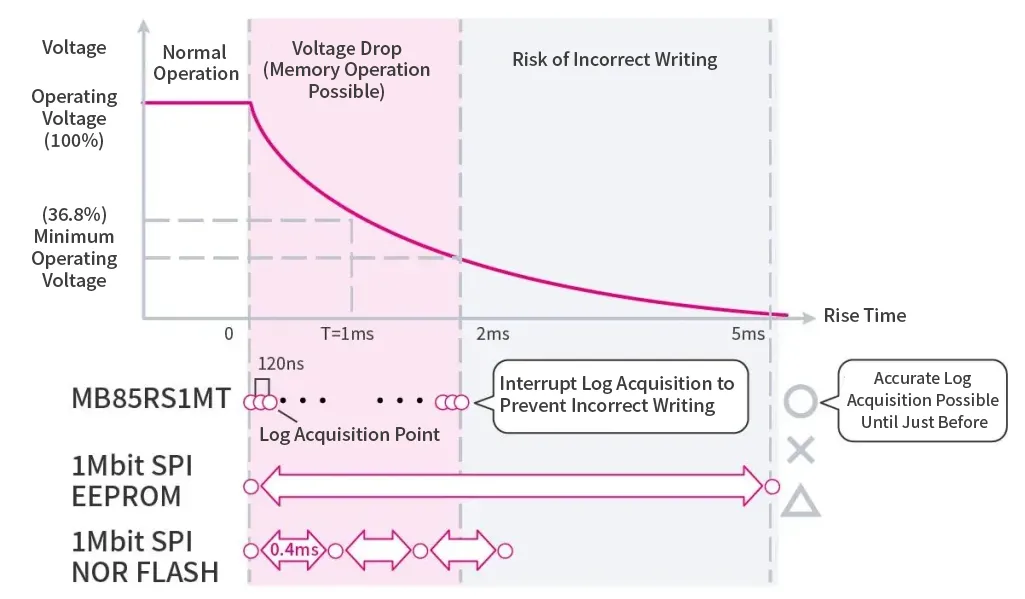
High Performance Nonvolatile Memory Conforming to J-EDR Regulations
The Ministry of Land, Infrastructure, Transport and Tourism (MLIT) is promoting the installation of EDRs that comply with the regulations as J-EDRs, and non-volatile memory is treated as a particularly important keyword in the technical requirements. Non-volatile memory is a component that electromagnetically records and stores dynamic and time-series data transmitted from on-board devices and does not require a power source to maintain the data. FeRAM is suitable for EDR applications because it is superior to EEPROM and FLASH memory, which are generally classified as non-volatile memory, in terms of high-speed writing and high write endurance, and can retain data even when the power supply is cut.
Capacity to retain acquisition data required for EDRs
The basic acquisition data specified in many EDR standards include front/rear speed change, displayed vehicle speed, accelerator pedal position, brake pedal position, engine start frequency, seat belt status, and warning lamp status. A sample rate of 100 samples/s for speed and 2 samples/s for other data is recommended, and these records can be handled with FeRAM capacity covering 64 Kbit to 4 Mbit.
The data elements required for J-EDR for which a sample rate per second is set are as follows. (taken from page 3 of the technical requirements for J-EDR by the Ministry of Land, Infrastructure, Transport and Tourism).
- Front/rear speed change: 100 samples/second
- Vehicle display speed: 2 samples/second
- Throttle position: 2 samples/second
- Brake on/off: 2 samples/second
Let us assume that the size of each data sample is roughly estimated to be 1 byte. If these are recorded for 5 seconds before the collision, the required capacity is as follows.
500+10+10+10 = 530 Byte = 4240 bit
The following data elements will be written here
- Maximum change in forward/backward speed
- Time until the maximum change occurs
- Ignition cycle, collision
- Ignition cycle, download
- Safety belt status, on/off
- All airbag warning lamps, on/off
- Time to airbag deployment