Applications
Electronic Paper Tag Applications in the Logistics Industry
Just in time with free location:
Free-location inventory management is realized by simultaneously providing wireless power supply and wireless communication.
Electronic paper tags are battery-less RFID tags with display functionality, enabling paperless use of paper labels used in logistics warehouses. Electronic paper tags are expected to be used as necessary labels for receiving and shipping management, sorting, and storage in logistics warehouses.
Table of Contents
About Electronic Paper Tags
The electronic paper tag is an RFID tag with a display function that uses UHF band RFID technology and operates without batteries. Since the electronic paper tag can repeatedly update its display content, there is no need to replace the label. Since the tag is battery-less and powered wirelessly by the reader/writer (R/W), there is no need to replace the batteries.
In the logistics industry, paper labels are often used because of the need to visualize information in many cases. Electronic paper tags not only display information in the same easy-to-read manner as paper labels, but also function as RFID tags, making it possible to go paperless. Barcodes and QR codes used in existing systems can also be displayed on electronic paper tags, making their introduction a smooth process.
Applications of Electronic Paper tags in the logistics industry
1. Receiving and shipping management in logistics warehouses
Paper labels are often used in logistics warehouses to manage incoming and outgoing shipments. Paper labels are easily soiled or damaged, resulting in reduced readability.
Printing and disposing of paper labels takes a lot of man-hours and is environmentally unfriendly. In addition, there are already cases in the logistics industry where RFID label tags (RFID tag + paper label) are used in combination with paper labels, since RFID tags cannot be visually checked to see what data is stored on them. Therefore, the same issues arise even if RFID label tags are used.
Since the electronic paper tag is an RFID tag with a display function, the above issues can be solved together. Further efficiency can be achieved by sharing with the logistics labels described below.
Issue | Solution |
---|---|
・Increased man-hours due to printing and disposal of paper labels ・Increased environmental impact due to paper label disposal ・Decreased readability due to soiling and damage in the warehouse |
・Paperless (carbon neutral and sustainable) ・Automatic rewriting of tickets in conjunction with the warehouse management system (WMS) ・Reduces environmental impact by being reusable ・Readability is maintained by wiping off soiled paper |
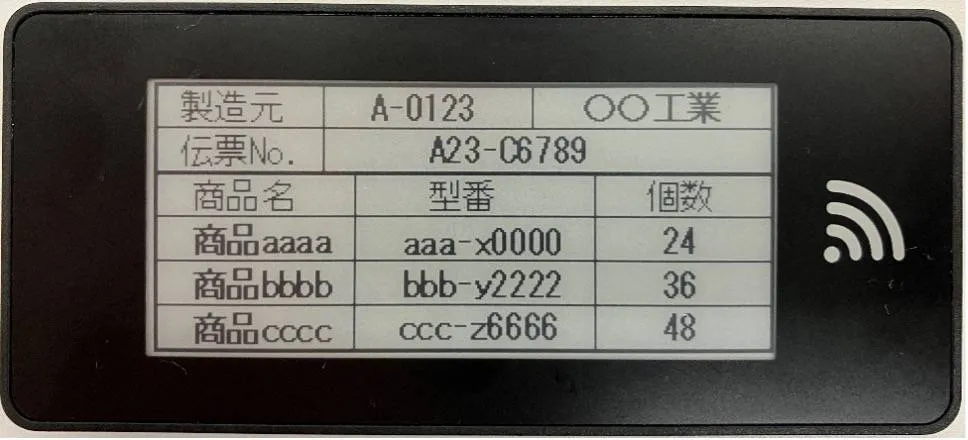
Electronic paper tag images of incoming and outgoing shipments in logistics warehouses
2. Use of Electronic Paper tags in logistics labels
Logistics labels used for sorting goods from distribution centers (warehouses) to individual stores are operated by attaching paper labels to containers and pallets. If they are operated by hand, entry errors may occur.
Even in the case of printed labels, mistakes can occur due to misdelivery if the label is forgotten to be removed. By introducing electronic paper tags, the system can be linked to the delivery management system, preventing delivery errors.
If barcodes or two-dimensional codes are used between companies, the existing system can continue to be used by displaying barcodes or two-dimensional codes on the electronic paper tags.
By using them as RFID tags, they can be operated in conjunction with the aforementioned management of incoming and outgoing shipments to further improve efficiency.
Issue | Solution |
---|---|
・Incorrect entry by handwriting ・Mistaken delivery by forgetting to peel off the label ・Increased man-hours due to printing and disposal of paper labels ・Increased environmental impact due to disposal of paper labels ・Decreased readability due to soiling and damage in warehouses |
・Paperless operation (carbon neutral, sustainability) ・Prevention of entry errors and erroneous deliveries by linking with a delivery management system ・Reduced environmental impact due to reusability ・Readability can be maintained by wiping off soiled paper. |
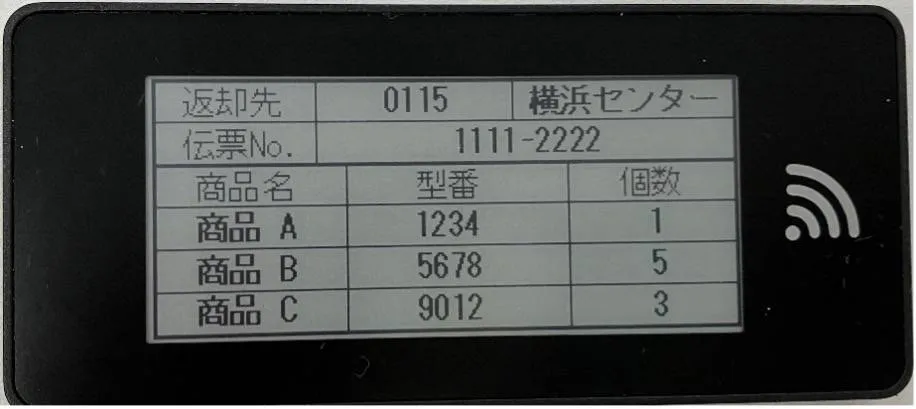
Electronic paper images of logistics labels
3. Management of shelves in a logistics warehouse
In warehouse product management shelves, keeping track of what is stored where is a key issue in improving the efficiency of receiving and shipping operations.
Goods in the warehouse are not always placed in a predetermined storage area, but are sometimes placed in an empty space. Therefore, when goods are released from the warehouse, it may take time to pick the necessary goods because the storage location is not known.
By attaching electronic paper tags to product management shelves, it is possible to visually check what is stored on the shelves, and in addition, by linking with the system during storage, it is possible to grasp storage information, which can be used as location management and improve picking efficiency.
Issue | Solution |
---|---|
・Picking work efficiency was lowered because it was not possible to identify where items were stored and on what shelves | ・By linking with the system, the work efficiency of product picking is improved |
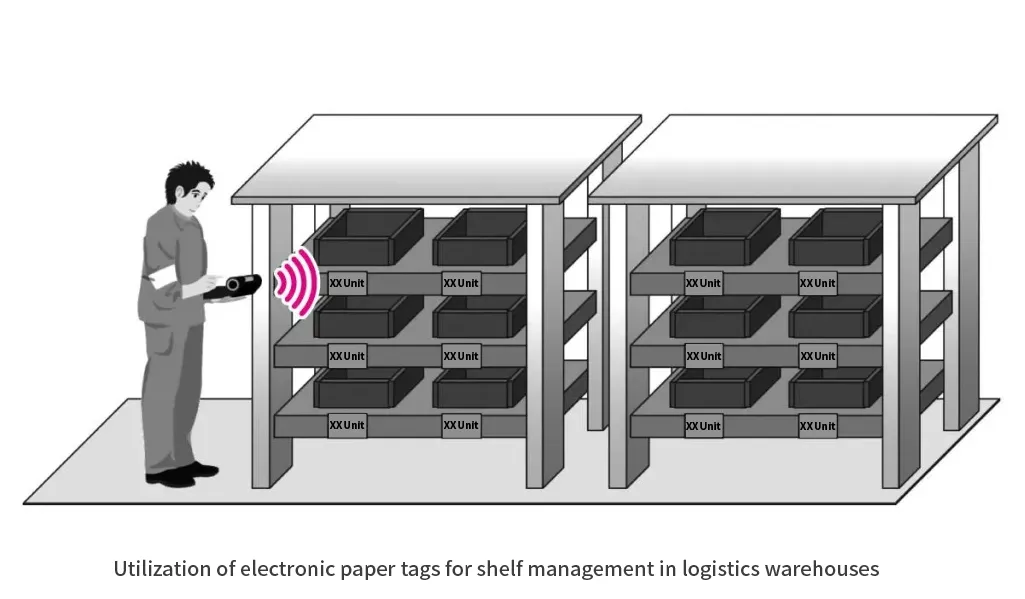
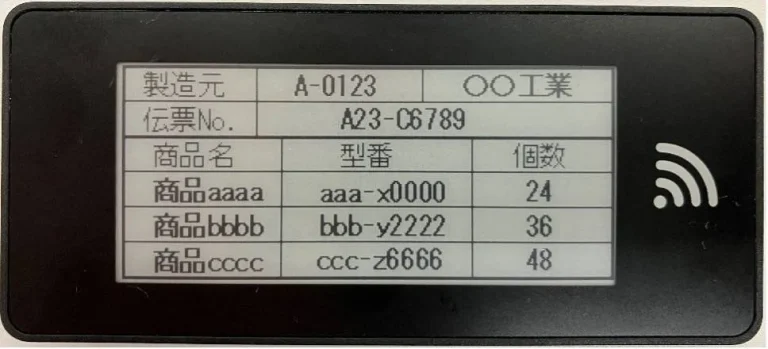
Electronic paper image of shelf management in a logistics warehouse